The Problem
Traditional shipping containers have not been upgraded since the explosion of eCommerce. Current shipping solutions are extremely susceptible to theft and contribute significantly to the annual tens of millions of tons of packaging waste.
The Skills
- 3D-printing
- Integration of electronics and mechanical components
- Integration of hard and soft-shell components
The Generate Project
Crate is a foldable, reusable shipping container that can prevent theft, promote sustainability, and improve customer engagement.
This was the second time that Crate was a Generate client. The previous Generate team created a hard-shell shipping container that folded down when not in use.
This semester, the client wanted a soft-shell shipping container, similar to envelopes or bags that you might receive clothing orders in. The team consisted of 5 mechanical engineers, 1 electrical engineer, and 1 product designer.
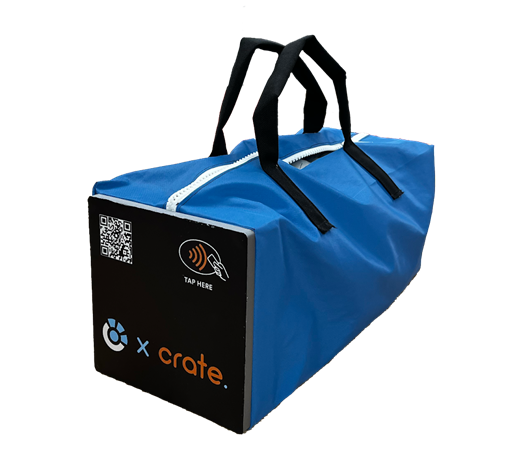
Our final Crate prototype
The Process
Requirements
- Must have two distinct states, one for in-use and one stackable for storage and charging
- Must lock and be unlockable by an app
- Must be GPS trackable
Main Challenges
- Creating a bag-like structure that would have a distinct "folded-down" state
- Protecting electronics in a soft-shell container
- Integrating a mechanical lock with an RFID controller
- Combining fabric with a hard electronics plate
- Sewing, a new skill for our team
The Result
Shape
We decided on the duffel bag shape with one hard side to hold the electronics. This was also the side the bag sits on and folds down to while not in use. That way we could have one hard side, which would safely house the electronics, and the rest would would be completely soft-shell and collapsible. The bag featured ironed pleats that would allow it to fold down neatly.
Electronics Integration
The electronics plate was actually comprised of a two plate system, which allowed us to clamp the fabric between the two plates. This allowed us to secure the hard plate to the organic material of the duffel fabric. The electronic components were mounted to the inside of the inner plate, concealing them from the inside of the bag, as well as protecting them from the outside.
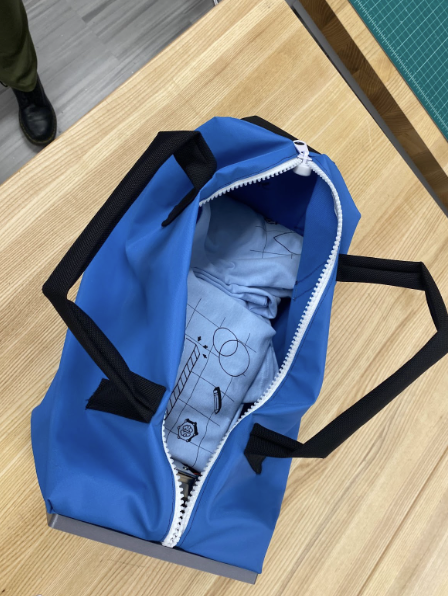
Duffle bag shape with hard bottom side
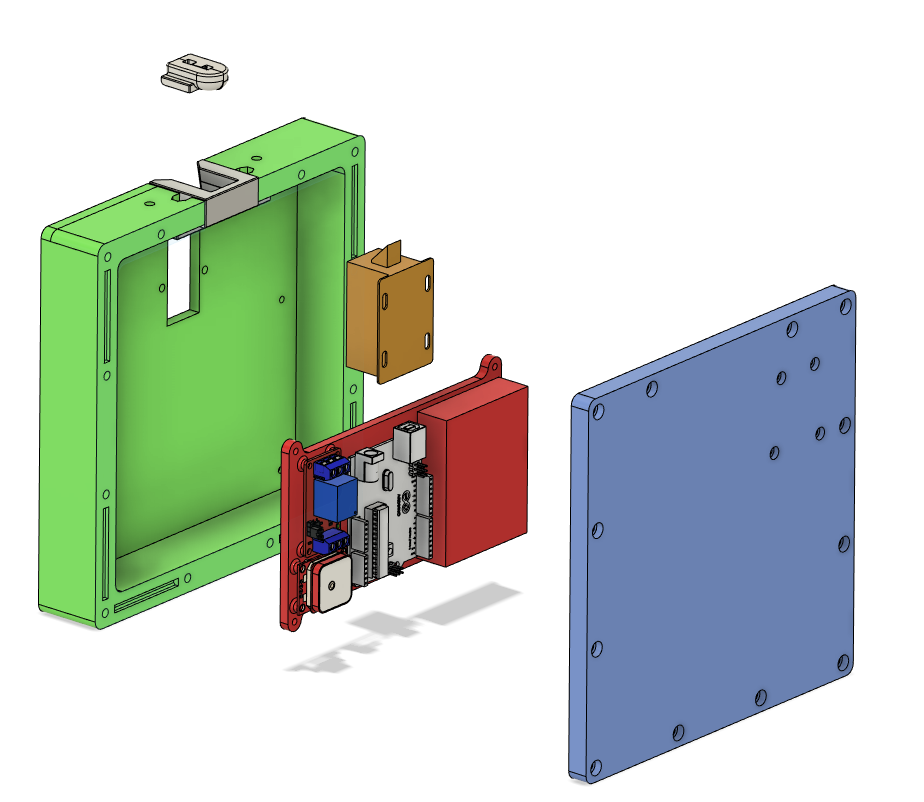
The green and blue plates are the two outer plates that clamp the fabric, while the red plate holds the electronics in between. The white part is the zipper attachment for the locking mechanism and the orange is the solenoid, which acts as the lock, as described below.
Locking Mechanism
The inspiration behind the locking mechanism was TSA-approved zipper-locks found on suitcases. These zippers are closed, clicked into place, and then locked mechanically. These zippers typically have a unique geometry to be able to fit into a specific lock.
Our solution was to modify the geometry of a typical zipper. To do this, I designed a part that would be attached to the bottom of the zipper (therefore concealed from the user), which would allow for this lockable geometry. When the zipper was in its closed position, this zipper attachment would fit into a slot inside the electronics plate. The attachment would then be secured into place by a solenoid actuator, which prevents the zipper from opening when it is in its actuated position.
Additionally, the actuator's geometry allows for the zipper attachment to move into the slot, but not back out without being lowered. This means the zipper can be locked into place without needing to actuate the solenoid, but can only be unlocked if the solenoid is actuated by the RFID signal.